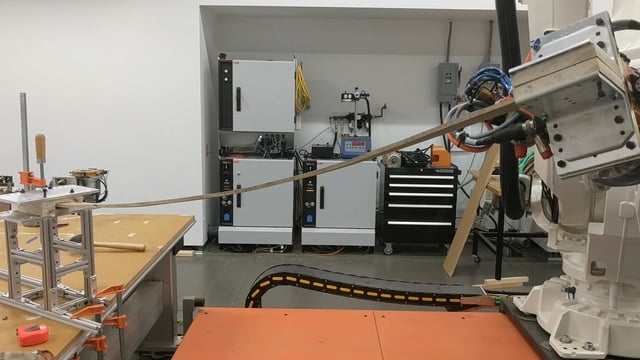


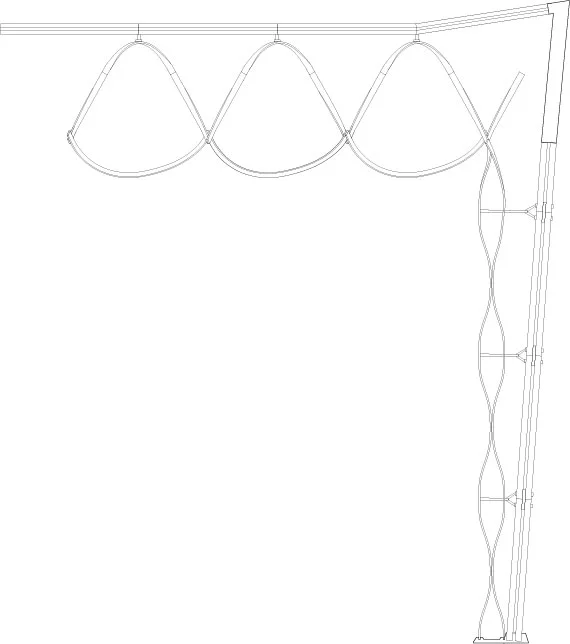
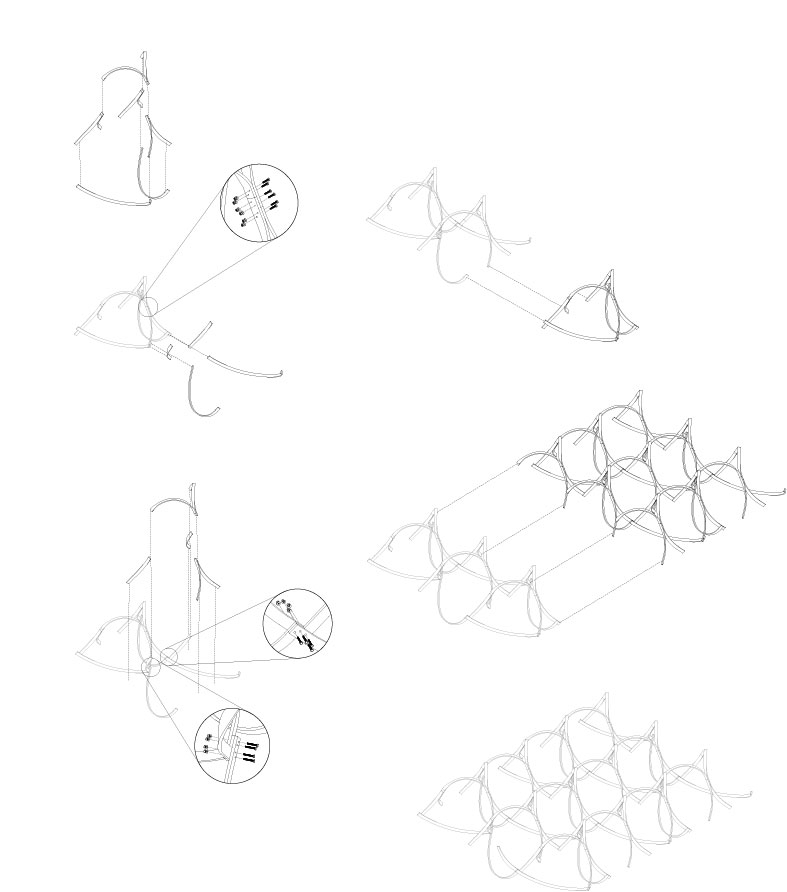


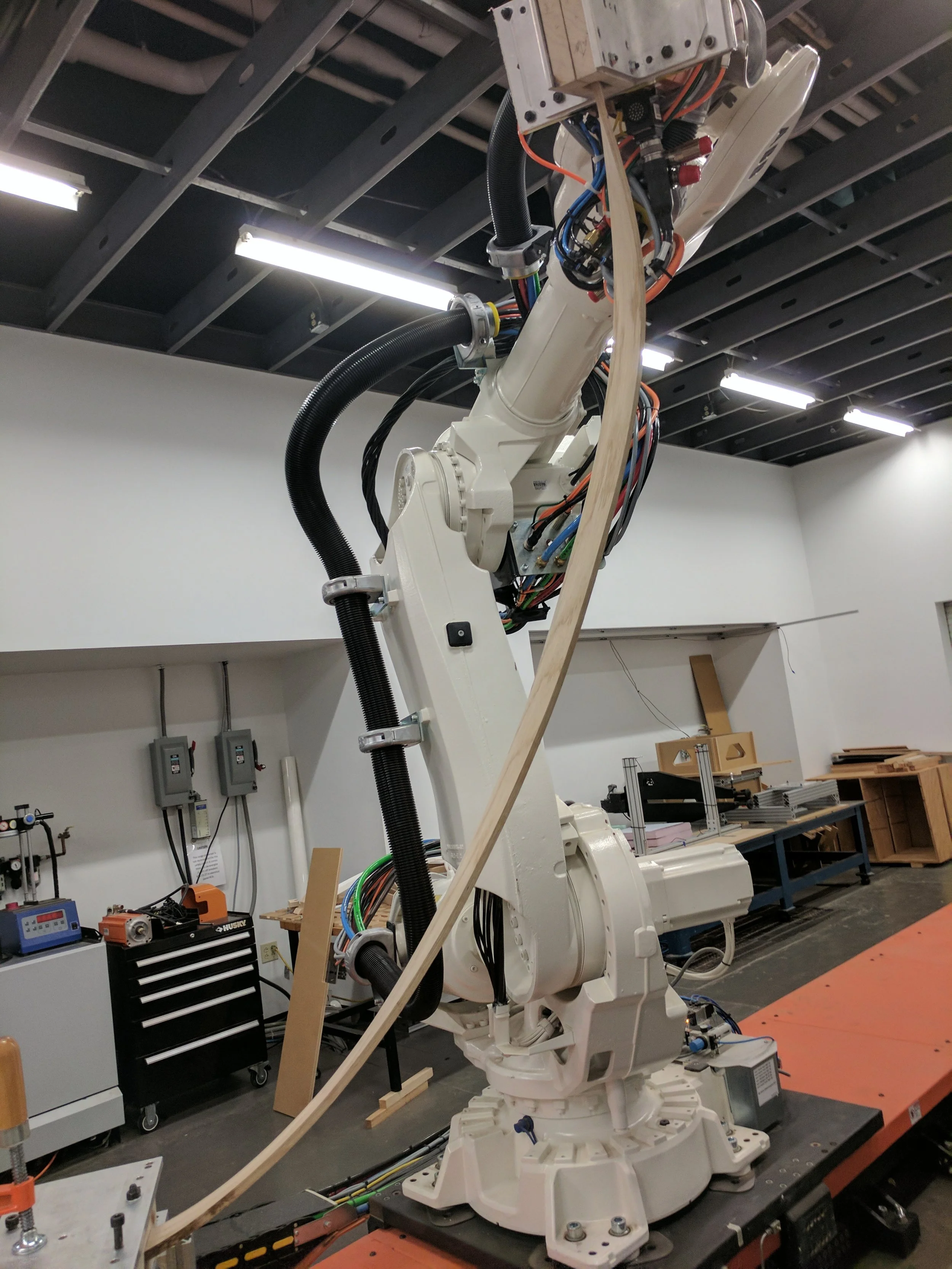
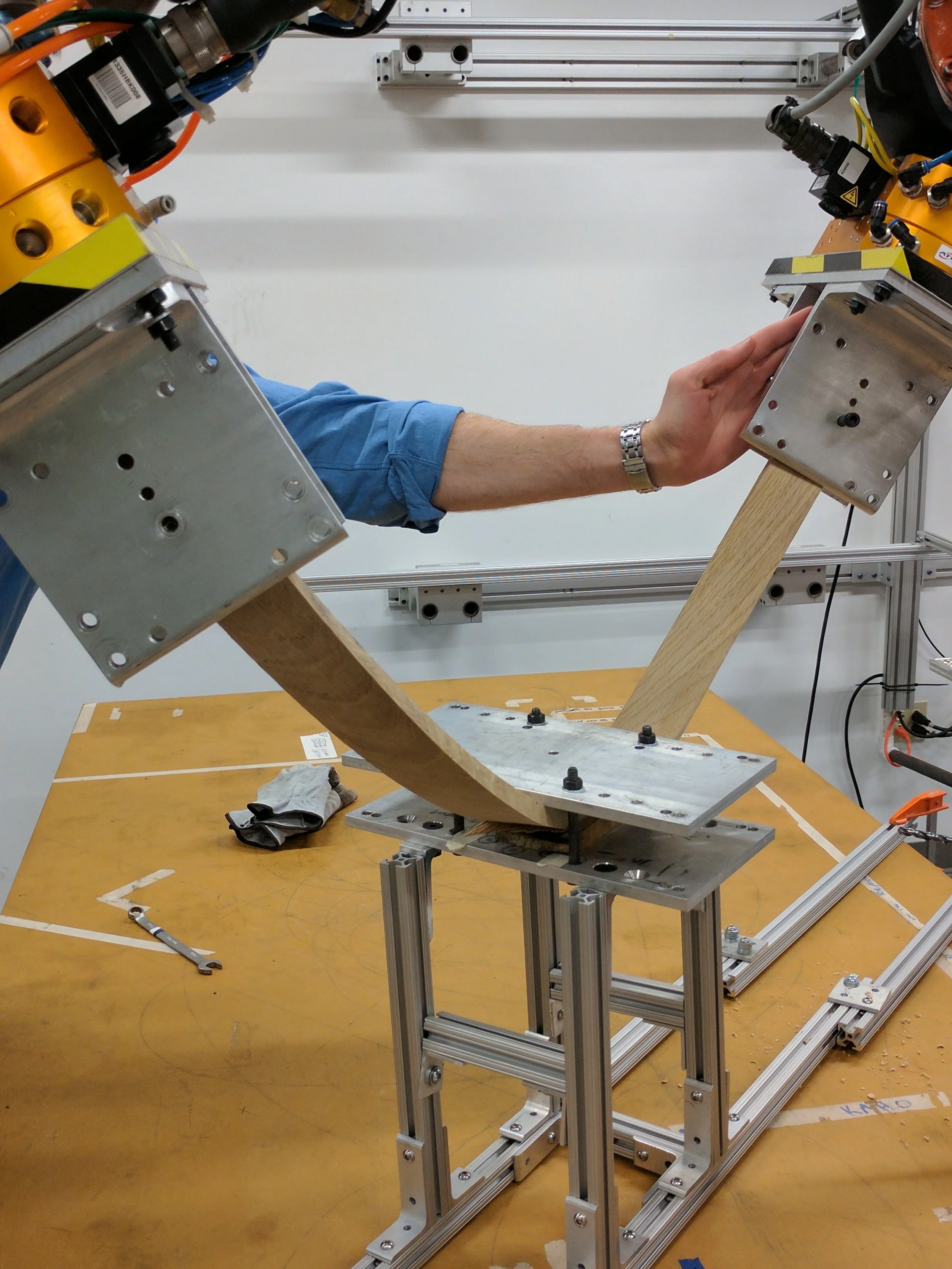


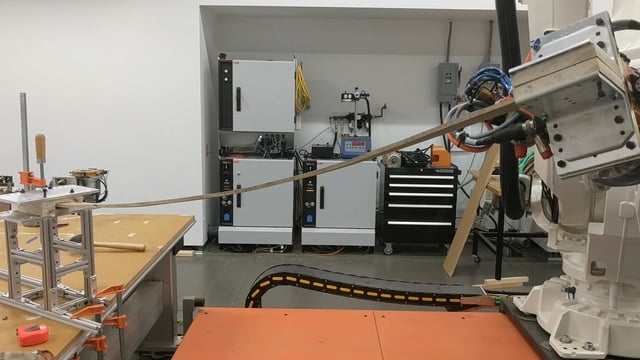
Documentation for Timber Studio Spring 2017 at CMU under Joshua Bard
Collaboration between me, Ai Fukuda, Trent Wimbiscus, and Jack Fogel.
This assortment of pictures and videos show how we tested different bending fixtures and setups and how we developed different bends and robot toolpaths in order to create the different unique parts we needed for the final truss assembly.
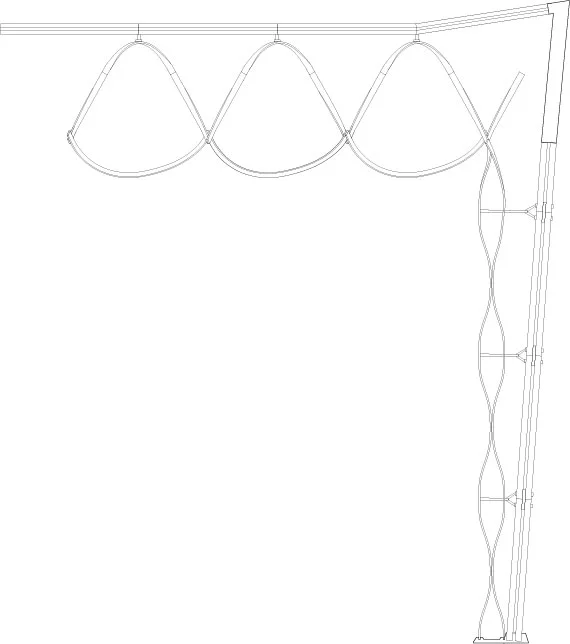
Enclosure wall detail showing how the truss would look attached to an enclosure and ceiling system.
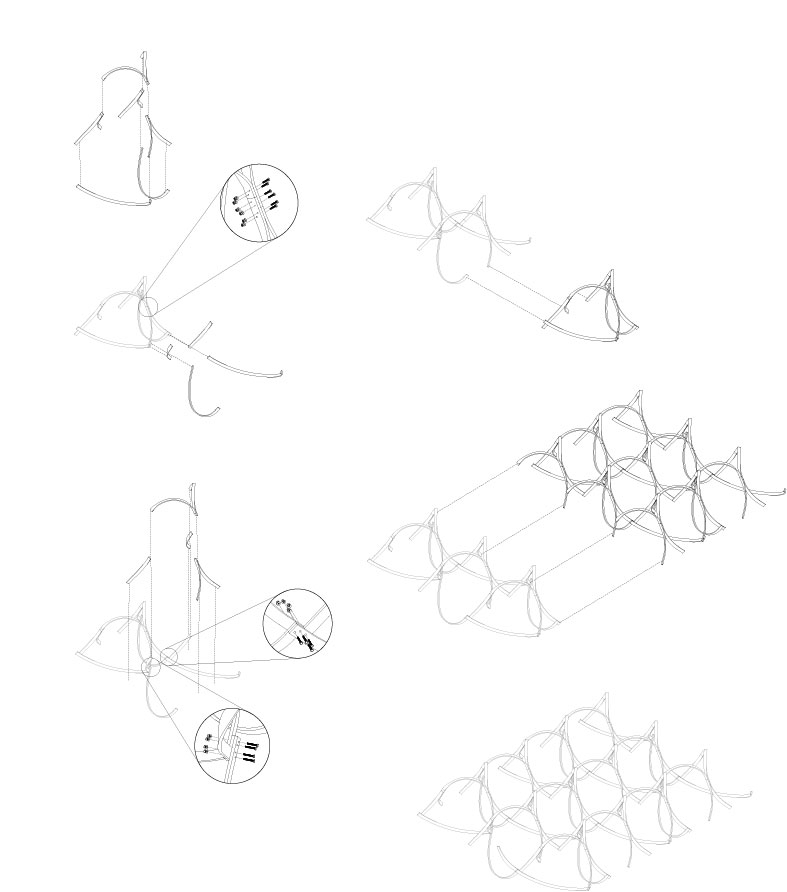
Exploded assembly drawing showing how the truss modules come together and also how different modules connect to each other to array in all directions.

Drying jig setup for the top half of the truss module pieces. This setup allows the steambent wood to dry in the right shape to be assembled into the final truss.
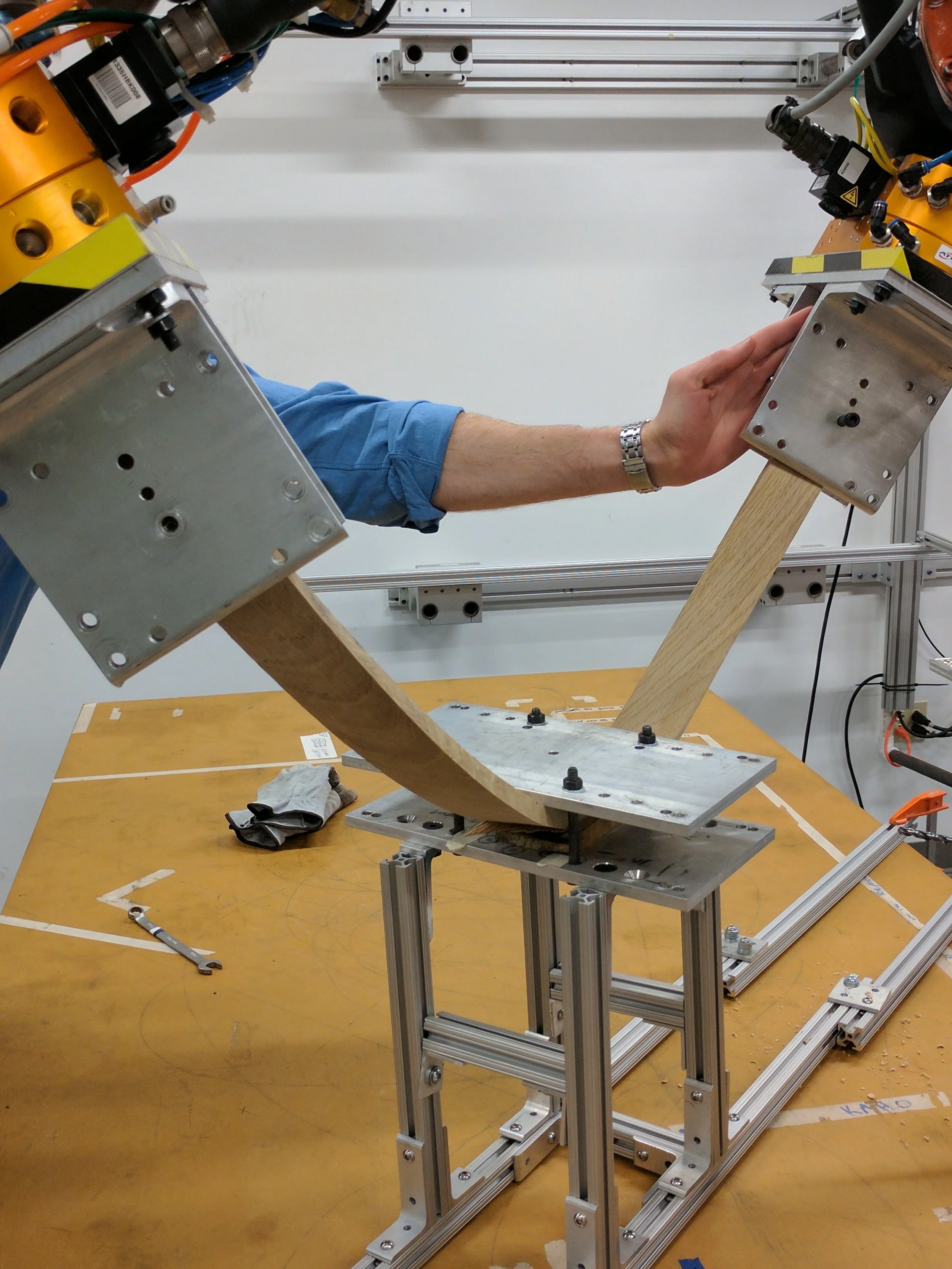
Top arch piece being bent by the robots using a fixture as a fixed center control point and the ends of the robots as the remaining 2 control points.